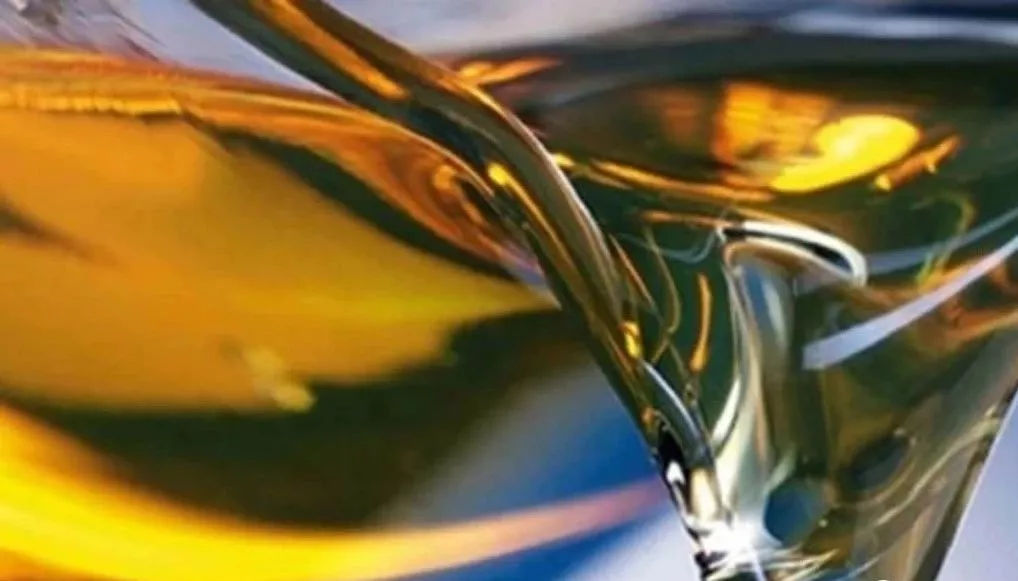
According to the formula of the oil product, the lubricant base oil components and additives will be added into the mixing kettle in proportion and order, and then mixed evenly by mechanical stirring (or compressed air stirring), avalanche pumping circulation, pipeline static mixing and other methods, and then qualified according to the product standard sampling analysis that is the official product.
Most of the lubricating oil blending is a homogeneous mixture of liquid-liquid phases dissolved in each other; in some cases, there are also liquid-liquid phase systems that do not dissolve in each other, and after blending, the lubricant is mixed with the liquid-liquid phase. Forms a liquid-liquid dispersion or, when the lubricant additive is a solid, a non-homogeneous mixture or dissolution of the liquid-solid phase system. The number of solid additives is not large, and eventually soluble in each other, forming a homogeneous phase.
It is generally believed that the liquid-liquid phase system homogeneous mixing is a combination of three diffusion mechanisms.
Molecular diffusion. The transfer of substances caused by the relative motion of molecules. This diffusion is carried out in the space of molecular scale.
Vortex Diffusion. When mechanical energy is transferred to a liquid material, the fluid at the interface of a high-speed fluid and a low-velocity fluid is strongly sheared to form a A large number of vortices, resulting from the transfer of matter due to the vortex splitting motion. This mixing process takes place in vortex-scale space.
Convective diffusion of the main body. Includes all matter transfer that is not part of molecular or vortex motion but causes a large range of all liquids to circulate, such as mixing The mass transfer process caused by convective circulation in the tank. This blending process is carried out in a large scale space.
The purpose of blending is to be able to adjust the lubricant variety, improve the lubricant quality, and ultimately get the desired lubricant. And in this process, what method, what equipment to choose, what methods to use to make the blending effect better, also appears to be Especially important.
1, Mechanical mixing and blending
The blended material is under the action of the agitator, forming the main convection and eddy current diffusion transfer, molecular diffusion transfer, so that the properties of all materials To achieve uniformity. The material in the tank will move in two directions when the agitator is rotating; one is the forward movement along the axis of the agitator, and the other is the forward movement along the axis of the agitator when it is hit by the wall of the tank. or the obstruction of the bottom of the tank, change the direction of its movement, after many changes of direction, the final formation of approximately circular flow; second is along the agitator The circular movement formed by the rotating direction of the pulp leaf makes the material roll over, and finally achieves the purpose of mixing evenly.
2, Pump circulation stirring and mixing
Pump the material from the bottom of the tank continuously, and then return to the reconciliation tank, under the action of the pump to form the main body of the convective diffusion and eddy current diffusion In order to improve the blending efficiency and reduce the energy consumption, the pump cycle blending method is constantly improved in the actual production. In order to improve the blending efficiency and reduce energy consumption, the pump cycle blending method is constantly improved in actual production.
3, Pulse stirring blending
Pulse mixing is to set the best pulse frequency, delay time and pressure according to different materials. By means of a set of special control devices on site and a collector plate installed in the reactor or blending tank, a powerful air flow is generated. Stirring from the bottom up, top down, evenly tuned in a very short period of time, speeding up and narrowing the reaction time to reach the Qualified product quality.
Continuous blending is to send the components of the blended lubricating oil, including the various base oils and additives needed, into the blending main pipe and mixer at the same time according to the proportion determined during product development, and the evenly blended oil product will come out from the other end, and its physical and chemical index and use performance will reach the predetermined requirements, and the oil product will be filled directly or entered into the finished oil tank for storage.
Factors affecting the quality of blending
Influence lubricating oil blending quality of many factors, blending equipment blending efficiency, blending component quality and so on all directly affect the blending of the Oil Quality. Here the main analysis of the process and operation of the factors on the blending of the oil quality after the impact.
1, the accurate measurement of components
Accurate dosing is essential for both intermittent and continuous compounding. Accurate metering is a guarantee that the components are fed in the correct proportions. Accurate metering of the component flow rate is essential for continuous blending. Inaccurate metering of the flow rate will result in misalignment of the component proportions and thus Affect the quality of blended products.
2, the water content in the component
Components containing water will have a direct impact on the turbidity of the blend and the appearance of the oil, and sometimes cause the hydrolysis of some additives, and reduce the effectiveness of the use of additives, so it should be prevented from mixing water in the components.
3, the air in the components
The presence of air in the component neutralization system is inevitable and can be very detrimental to the blend. The presence of air may not only promote additive reactions and deterioration of the oil, but also lead to poor component metering due to the presence of air bubbles. Accurate, affect the correct proportion of components.
4, the temperature of the reconciliation component
To choose the appropriate blending temperature, the temperature is too high may cause the oxidation of oil and additives or thermal deterioration, low temperature components of the fluidity of the components can deteriorate and affect the effect, generally 55-65 ℃ is appropriate.
5, the dilution of additives
Some additives are very viscous, before use must be melted, diluted, modulated into the right concentration of additive masterbatch, otherwise it may affect the uniformity of the blend, and may affect the accuracy of measurement, but additive masterbatch should not be added to the diluent too much, so as not to affect the quality of the lubricant product.
6, the cleanliness of the blending system
The presence of solid impurities in the blending system and non-blending components of the base oil and additives are all contaminants to the system and can cause The quality of the blended product is substandard, so the lubricating oil blending system should be kept clean. From an economic point of view, the possibility of blending only one product in a system is extremely small, so the contamination of the system by non-blended components is a major concern. Inevitably, on the one hand, the actual production should try to clean up the pollutants, and on the other hand, similar quality and variety of oil should be arranged in a System blending to ensure the quality of blended products.
7, Mixing time
According to the size of the mixing kettle, the amount of mixing materials, heating temperature, stirring mode and other reasonable to determine the stirring time, stirring time is too short, mixing is not uniform enough; halving time is too long, energy consumption.
Click to buy a lubricating oil blending line